Solution 1 - Optimizing the blast furnace
In the BF/BOF, iron ore is reduced with the help of coking coal
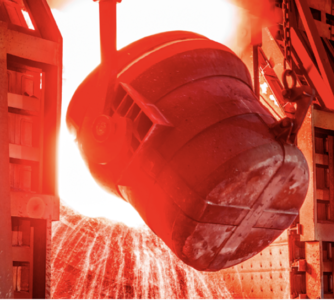
In nature, iron occurs in the form of ore. In mining, the ore is extracted from the rock and processed. To turn the ore into iron, it is reduced and melted in a blast furnace with coke at around 2,000 °C. The resulting iron ore contains more than 2% carbon and cannot be used for products in this form. The iron ore obtained is therefore processed into crude steel in the converter using oxygen and cooling scrap. The cast slabs are then rolled out in the hot rolling mill and, if necessary, further refined and the surfaces coated.
According to the example calculation in ISO 14404.1, crude steel production generates 2,387 tons of CO2. Modern and optimized blast furnaces can save up to 20 %.
Around 70 % of crude steel is produced using this process. It is the established mass production process for crude steel.
The disadvantage of the process is the CO2 produced. There are already possibilities for optimisation, which are usually verified using mass balance methods, as physical separation in the blast furnace/converter process cannot be implemented.
Optimizing the blast furnace route in steel production can reduce CO2-emissions and is crucial to tackling the climate crisis. Here are some ways in which this optimization can be achieved:
- Use of hydrogen-rich reducing agents: The traditional use of coking coal as a reducing agent in the blast furnace process leads to significant CO2-emissions. CO2-emissions can be significantly reduced by using hydrogen-rich reducing agents such as green hydrogen.
- Improvement in fuel efficiency: Optimizing combustion in the blast furnace can increase energy efficiency and reduce CO2-emissions. This can be achieved through better air and fuel distribution and the use of modern burner technologies.
- CCS (Carbon Capture and Storage): The integration of CCS technologies in blast furnace plants makes it possible to capture and store CO2-emissions instead of releasing them into the atmosphere.
- Electrification of processes: The use of electric arc furnaces instead of blast furnaces makes it possible to use electrical energy from renewable sources and minimize CO2-emissions.
- Use of renewable energy: The use of renewable energies such as wind and solar power to generate electricity in steel production can significantly reduce the carbon footprint.
- Recycling and circular economy: The increased use of recycled materials and the promotion of the circular economy help to reduce the need for new steel production and thus lower CO2-emissions.
- Process optimization and heat recovery: Optimizing the processes in blast furnace plants and heat recovery can reduce energy consumption and increase efficiency.
- Research and development: The continuous research and development of new technologies and processes for low-CO2 or CO2-free steel production is of crucial importance.